David Wells, vintage pen collector and dealer of primarily British
writing instruments presents this discussion on a delicate material used
by several pen companies in the past. Before the introduction of colourful
resins and celluloid materials, fountain pens were made from vulcanised
rubber with colour variations limited mostly to black , red or a variation
of the two we call mottled, ripples or wood grains. Casein material was
one of the first alternatives to provide a wide variation of colour and
patterns.
What is casein?
Casein-formaldehyde is the generic name for an early plastic of natural
protein origin, this protein being casein, as found in milk, although
it is also found in horn, and vegetable products such as soy beans, wheat,
etc. The plastic is normally referred to simply as casein.
Who discovered casein formaldehyde?
The first casein formaldehyde process was developed by Adolph
Spitteler and W. Kirsch, who used whey and formaldehyde and tested the
action of enzymes. Krisch, head of a large firm of printers in Hanover
experimented with casein to make a washable white board for replacing
the slates used in school - paper was too expensive at that time for use
by children to practise writing. He collaborated with Adolf Spitteler,
a chemist in Bavaria and on July 15th 1899, a patent for "plastic
compositions" was awarded in Germany.
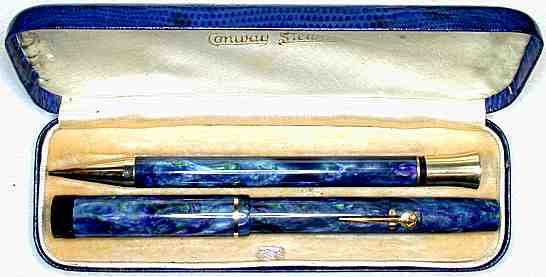
A vintage Conway Stewart 211 boxed set (Photo
David Wells)
The Manufacturing History of casein.
The patent was taken up by firms in Germany (Vereinigten Gummivarenfabriken,
at its factory in Harburg) and in France by Pellerin and Orosdi (Compagnie
Francaise de la Galalithe, at Levallois Perret). The product was introduced
under the trade name Galalith and was first shown at the Paris Universal
Exhibition in 1900. A lot of development work was still required to produce
a stable material, and the two companies merged in 1904 to form the International
Galalith Gesellschaft Hoff and Company with a new factory in Harburg.
A process starting with dried casein granules, known as the dry process,
was developed and this was to become the universally adopted method for
casein plastics manufacture and remained virtually unchanged throughout
its history.
In Britain, a wet process starting with milk curds was patented in 1909
by Victor Schutze, a Russian student from Riga. This material was called
Syrolit and a factory of the same name was set up in a disused cloth mill
at Stroud in Gloucestershire. However, it was not successful and by 1913
the company was bankrupt. A new company was established at the same premises
to manufacture casein using the dry process. The new product was called
Erinoid and this was also adopted as the name of the company. Production
commenced in 1914 and as supplies of Galalith were cut off at the commencement
of World War I, the material found a ready market and button manufacturers
from Birmingham were waiting on the doorstep for the first consignments.
Lactoid, made by BX Plastics was introduced in 1922 at their Larkswood
Factory in Higham Station Avenue, London. Young & Wolf Ltd. had a
small production unit located at Bridgend Works, Stonehouse in Gloucestershire
- they manufactured mainly rod, button blanks and knitting needles from
about 1930.Young and Wolf pioneered the slicing of casein button blanks
from rod in the UK. Charles Horner Ltd. of Halifax, England, like Young
& Wolf, also produced casein plastics mainly in the form of knitting
needles, button blanks and rod. Their brand name was Dorcasine.
These four British manufacturers formed the Casein Plastics Association
(until 1938 it was called the Artificial Horn Manufacturers Association).
At the commencement of World War II supplies of raw casein granules were
no longer obtainable from Europe, the traditional source, and the CPA
were encouraged by the British Government to seek alternative supplies
in order to make buttons for military use. Argentina provided this need.
In 1944, the CPA co-operated with The Knitting Pin Association and the
Casein Button Manufacturers Association to form The Casein Plastics Joint
Development Association, to represent the interests of both manufacturers
and users of casein plastics. Perhaps the greatest contribution of the
CPA was in the 1950s to improve the process for manufacturing casein granules.
With the co-operation of the New Zealand and Norwegian dairies, this resulted
in casein of improved quality with a better base colour thus increasing
the colour range, especially of very pale colours.
Erinoid remained the major producer of casein plastics in the UK until
they stopped manufacture in about 1980. At that time they were part of
British Petroleum. There were negotiations in hand for the sale of the
casein business, which was still profitable, but unfortunately these broke
down. BX Plastics had already closed their Lactoid business in 1962 and
all other British casein firms had also ceased production.
In the United States, casein plastics material was introduced by Christensen
about 1919 and sold under the name Aladdinite. In 1924, Karolith was produced
followed by Erinoid by a subsidiary of the British company. Casein did
not achieve the same success in the US as it did in Europe - partly due
to greater competition from cast phenolic resins, also some European applications
were excluded because of the climatic conditions. Starting in about 1928
many casein manufacturing plants joined forces with button manufacturers
to make casein directly into buttons. This included button manufacturer
George Morrell who took over Kyloid, and Aladdinite who joined the Button
Corporation of America. In 1931 Karolith Corporation, Erinoid Company
of America, American Machine & Foundry Company and Pan plastics Corporation
merged their casein interests to form the American Plastics Corporation
to produce casein under the name Ameroid.
References:
David Wells Vintage Pens
Jonathan
Donahaye Conway Stewart Collection
Conway
Stewart history
Home of the Plastics Historical Society
|