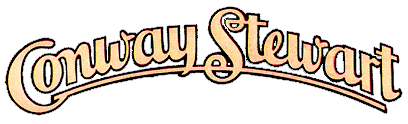
This is not a list of instructions on how to repair vintage Conway Stewarts,
but rather an explanation as to how I do the work myself. This frees me from the
danger of facing a million dollar law suite if you manage to botch your repair
and destroy a valuable pen.
So for starters, never make your first repair on a valuable pen. Do it on
one you intend to cannibalise for parts!
1. Cap
1.1 Removing the clip:
When I can, I always like to remove the clip, since this enables one to remove
scratches and polish the cap without being inconvenienced by the clip. However,
this process is only essential when, either you have to replace the clip, or it
is badly bent and must be reshaped.
For pre-1935 pens with fixed clips, I have never tried to remove the clip
and don't advise it. If you have such a pen with a missing clip, a spare clip
can easily be super-glued into the two staple holes, but I have only twice done
this, due to the extreme rarity of spare clips.
For pre-1949 pens where the washer clip is held in place by a flat-top or
peaked-top, the top, which is made of Vulcanite (hard-rubber), must be removed.
This is sometimes very stubborn and difficult to unscrew when it is plugged up
with dry ink. My method of unscrewing is to use a pair of pliers to which, long-ago
,I filed down the teeth. Each time I use them I prepare a wad of facial tissue
paper by folding it until I have a 20 x 1 cm strip. I wrap this strip once round
the top of the cap and then apply pressure with the jaws of the pliers. The paper
strip prevents the jaws of the pliers from scoring the top. If I am unable to
turn the top with simple pressure, I prepare a cup of water, as close to boiling
as possible, and dip the cap, top downwards into the cup, for about 30 seconds.
I then immediately re-wrap the paper round the top and try the pliers trick again.
If it doesn't budge a second time I repeat the process until it does. Through
downright stubbornness I have never failed over the several hundred times I have
done this. I use this method also to remove the tops from Casein pens because
the water treatment is never prolonged enough to distort the Casein. Warning!
This procedure usually makes the cap turn from black to yellow brown – a
common phenomenon with Vulcanite. However, since I always polish my pens (see
on) before reassembling them, and since this is a surface effect, there is no
difficulty in re-obtaining the jet black of the original.
Post 1945 pens: these are the pens where the clips are attached to the cap
with a black, brass or aluminium screw-in stud that may or may not be fixed on
the inside of the cap by a nut. Let's take the first case where the stud screws
into the plastic top of the cap and does not pierce through into the inner cap.
Pens such as the CS58 and 60 series are typical but you can always check this
by inserting a light into the cap to see if there is a screw thread and nut at
the top. For these pens the first thing is to try and rotate the clip. Sometimes
the clip rotates with the stud, but do not use force. You may distort or even
break the clip. The next step is to use the hot water treatment and then place
the cap stud-down on to a piece of latex or some-such (I use an old computer mouse
pad). Press down and rotate. How the water treatment acts in this case I don't
quite know. Perhaps the differential expansion and contraction of the metal and
the plastic breaks the "seal". On occasions I have observed air-bubbles
arising from beneath the stud under water giving sign that something has happened.
Sometimes this procedure works, but if it fails, either you give-up, or attempt
the next method which is very dangerous! For this procedure you need a pair of
parallel jaw pliers. You grab tight the narrow shelf or rim at the periphery of
the stud with the pliers and rotate. Here the great peril is that the pliers tend
to slip off the rim thereby scoring the stud. If this doesn't work, nothing will.
I only use this method when I have spare studs at hand. I rate my successes for
removing these clips at about 70%
For caps where the stud pierces the cap and is held in place by a nut (eg
CS 60L, 36, 84 550, 560) , the objective is to remove the nut. To do this you
need to prepare a series of screw drivers of different widths that are used to
unscrew the nut inside the cap. I prepared my screw- drivers by filing a U shaped
gap in the centre. This is not too easy because the steel is very hard. Before
trying to unscrew the nut, the inside of the cap should be thoroughly cleaned
by immersing in water and then using a pipe-brush. There is no immersion problem
because none of these pens (except CS12) are made from Casein. The main difficulty
is in the frequent cases where the screw and nut are corroded. In this situation
nothing on earth will enable you to succeed. Either you must accept your failure
and keep the pen as-is, or abandon it to the Frankenpen scrap-heap. (You can saw
off the top of the cap and in this way retrieve the stud and clip). I would say
my success here is about 30% -derived mainly from pens that have been little used.
1.2 Cap bands:
If you want to remove scratches from the cap you must be very careful not to remove
gold-plating from the bands. I have never seen brassing on CS 60 or CS58 pens
and believe them to be solid gold. Also several early models have 9 or 18ct imprinted
on the bands but I believe that the bands on most pens are plated. Therefore I
am careful to keep the wet-and-dry silicon carbide paper away from the bands.
Sometimes I carefully mask the bands with Scotch tape, but even then one has to
check the masking itself to verify that the tape has not been rubbed off.
1.3 Clips:
You may want to re-plate the clips, because the CS plating on the clips is notoriously
thin. If you have a good gold-plater giving cheap rates, I would love to know
about it. More often you will want to bend the clip back into position and ensure
that it touches the cap at its lower point. I find that the easiest way to remove
bends is with my parallel–jawed pliers held longitudinally over the clip.
This gives me maximum control of the pressure I need to exert.
1.4 Worn threads:
Sometimes the pen cap does not thread well on to the barrel, either due to distortion
or more often because of constant use. In the earlier pens with Vulcanite tops
this can easily be rectified by shortening the inner cylindrical part of the top
so as to reduce the distance from its lip to the top of the section. In this way
the upper part of the cap thread now comes into play. Of course, if too much is
ground off then the nib will touch the inner roof of the top with disastrous consequences.
2. Section
2.1 Removing the section:
I always remove the section from the barrel in order to clean the pen. I do this
using the same method as that for removing the top of the cap. The danger in this
process is that by forcing the pliers one risks cracking the thread of the barrel
resulting in the virtual death of the pen. This is specially true for Dinkies
so go carefully. I have never failed to remove the section, but the most stubborn
cases are usually Casein ones. This is because the Casein barrel will shrink as
its moisture content comes into equilibrium with the relative humidity of the
air. Soaking the section and barrel tip FOR A SHORT TIME in water will allow the
Casein to absorb water and its diameter to expand.
Once the section is removed, the feed should be knocked out as per "Da
Book" by Frank Dubiel. Here again some sections can be stubborn but soaking
does the trick. I then clean up the feed and section to a point where the feed
can be inserted easily into the section and removed freely by hand. Unless this
is so it can be difficult to insert and correctly adjust the position of the nib.
3. Barrel
3.1 De-saccing and re-saccing:
The dried-up sac should be removed. This I do using a dentist's pick, taking great
care not to damage the J-bar of models using this system, such as the Dinkies
and many early models. If we are dealing with a floating pressure bar adhering
to the sac these can be easily removed together. .Re-saccing onto the section
is as per Dubiel, but I always use as narrow a gauge of sac as I can, in order
to improve ink-flow.
3.2 Changing the lever:
This is great fun, but first of course you have to have a spare lever taken from
a rubbish pen. To do this I first remove the pressure bar. The floating pressure
bar can be removed by pulling it out using a pair of long-nosed pliers. The J-bars
can be removed by grabbing the bar and pulling it out by a movement that rotates
the bar within the barrel. Otherwise you can remove the bar by sawing across the
barrel about 1 cm from its base cutting from the side opposite the lever so as
not to cut through the bar. Then, pull the bar straight out. Now, open the lever
to its vertical position and saw through the barrel close to the lever axel. The
last bit of plastic can be snapped off the barrel by hand. You should now use
a pair of small stub-nosed pliers to break-off the plastic until the inner steel
ring that holds the barrel in the inner groove of the barrel is revealed. You
can then pull out the lever, with its ring in place, threaded through the hole
in the axel.
Next, the broken lever of the pen you want to restore must be removed. To
do this you have to push the broken lever into the barrel. It is often not easy
and requires quite a lot of force, but the lever will give way long before the
barrel breaks so perseverance is the name of the game. Once inside the barrel,
the lever plus its ring must be hooked out from the mouth of the barrel. Don't
throw it away!
It should be realised that there are several lever models and only the correct
one may be used. I have yet to replace a flange lever so I cannot comment on pre
1935 levers. In post 1935 pens most levers look the same but the position of the
hole holding the wire ring is different. Check this and the length of your new
lever with the old lever just removed. Don't in any circumstance use a wrong lever.
The difference in position of the holes may be less than a millimetre but it is
critical.
Check that the steel ring is not too rusted and that it is not distorted.
The ring is doubled and its opening point should be opposite the threading hole.
Now check that the diameter of the ring is equal to or less than that of the barrel.
(Preferably it should be less because it will open out a bit when inside the barrel).
You will never be able to get the lever into place using a large diameter ring
and will probably ruin the lever in the process. I am told that the G string of
a steel stringed guitar is suitable for making rings though I have never tried
it. If the ring is too big, either replace it, or you may be able to reduce its
diameter, but do not deform it. Lastly check the two outwards pointing teeth at
the end of the lever. These teeth slide into the grooves of the pressure bar and
must be uniform in shape and position. Best to try them on the intended bar to
see that they slide into the bar and are not too loose.
Now for the hard part. You have to push the lever on its side (transversely)
through the lever-hole holding the lollipop end outside. I then try to push the
lever to the top (section) end of the barrel. The lever must be pushed in until
the widened part pierced by the ring-hole is inside the barrel. Then the lever
must be twisted round so that the top face of the lever is in alignment with the
length of the barrel. This may hurt your fingers but you should on no account
make use of pliers to twist the lever. If it won't twist by hand it will bend
if pliers is applied.
Once aligned the lever should be pulled back to the center of the lever hole
and can be pushed back and forth until you feel that the ring slips into the circular
groove inside the barrel. I check this using a torch in the barrel to see that
the ring does not protrude, and if it does, a dentist's pick can be used to push
the offending part of the ring into place. Check that the lever opens and closes
easily and hey presto, job done! If on closing the lever it does not click into
place, all is not lost. Check where the contact between lever and barrel groove
is causing friction and slightly file away the offending surface using a needle
file. I have found that if it is at the lollipop end, the ridge beneath the lollipop
can be filed down, but great care must be taken not to damage the lollipop because
this is the weakest part of the lever, and the part where the greatest pressure
is exerted during ink-filling.
Now, all you have to do is to replace the pressure bar. There are several
sizes of pressure bar, so if you still have the original one, use it. Note that
the length of the pressure bar at the section end is shorter than the length facing
the bottom of the barrel. Open the lever to an angle of 45 degrees, and with the
long-nosed pliers push the pressure bar into the barrel so that the teeth of the
lever slide into the grooves of the pressure bar. Push the pressure bar in until
it reaches the stop position and your done. Success success! But if at first you
don't succeed, try again.
4. Clean-up
I won't try to compete with methods used elsewhere ("Da book " etc).
So I'll just make a few comments here. The imprints must be masked. I do this
with Scotch tape, which stands up well to abrasion. However, do not forget to
mask the "Made in England" imprint or the "Patent No." imprint
which is often placed across the barrel beneath the major imprint.
For scratches I start with wet No. 800, 1,000 or even 1,200 grit according
to depth of scratch. I then move to older pieces of 1,200 grit which give a finer
polish, and I do the final work using a white buffing composition on a buffing
wheel. For deep scratches, I fill them with super glue, wait 24 hours and then
move up the grits as above.
Here endeth my lightening overview on Conway Stewart
repairs.
Links:
Jonathan Donahaye
Conway Stewart Collection
Conway
Stewart history
|